Policy
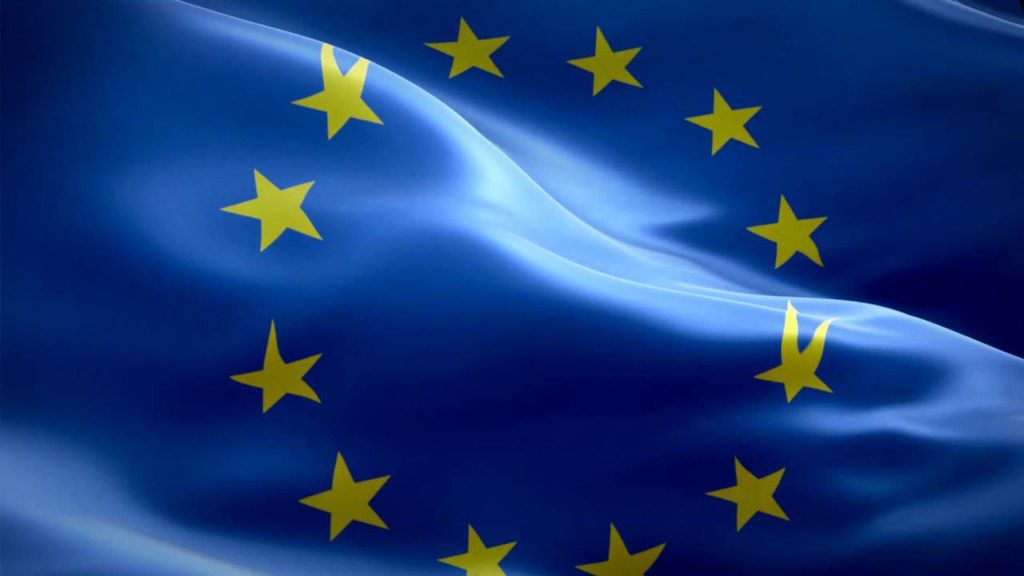
Policy
Home Policy
Eurovent represents the common interests of the HVACR industry in the development of European and global policy and legislation. We advocate for policies that strengthen the EU Single Market and level the playing field globally, stimulate innovation and Europe’s industrial competitiveness in the green and digital transitions, and unlock the potential of our sector to improve quality of life and contribute to a net-zero future.
Overview of core Policy Issues Eurovent cares about
General
This section provides updates on general topics that do not fall under any of the core Policy Issues outlined above. It moreover includes a historical archive of Eurovent’s GEN Documents, which was a form of providing information to our members in the past.